How to Set Up a Preventive Maintenance Schedule That Lasts
published
16.6.2024
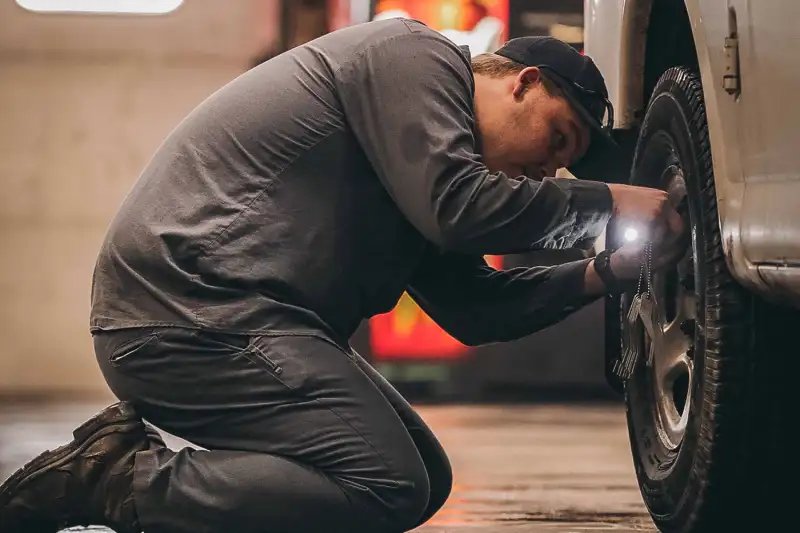
Don't wait for breakdowns! Create a lasting preventive maintenance schedule for your heavy-duty trucks. Get tips for assessing needs, creating tasks, & keeping your fleet running smoothly.
date
Author
Reading Time
An ounce of prevention is worth a pound of cure, and that has never been truer for heavy-duty vehicles. Staying ahead of issues allows you to run a safe, efficient operation and avoid expensive repairs and unscheduled downtime. The best way to do this is with a comprehensive preventive maintenance schedule.
It may seem like a tedious, time-consuming, and even expensive outlay, but every second and penny you invest in preventive maintenance is worth its weight in gold. Here, you will find everything you need to create a preventive maintenance schedule that actually lasts!
Understanding Preventive Maintenance
Preventive maintenance is the scheduled maintenance of vehicles before problems occur. This helps to identify and resolve any potential issues before they turn into costly repairs and unnecessary operational downtime. Unlike reactive maintenance, which addresses issues as they arise, preventive maintenance is planned and routine and aims to prevent these issues from developing in the first place.
This is an essential part of care, and every minute your vehicles aren’t on the road costs you money. It not only improves operational efficiency but also boosts safety on the road. The likelihood of mechanical failure that could lead to accidents is lessened, creating safer roads for everyone involved.
Assessing Your Needs
Determining your fleet's precise maintenance needs involves a detailed assessment of your vehicles' types, usage patterns, and operational requirements. Factors such as the following need to be considered when assessing your needs:
- Mileage
- Engine hours
- Loads carried
- Types of operations (towing, etc.)
- Number of stops made
- Environmental conditions (on-road vs off-road, urban vs rural driving)
Seasonal changes are also something that greatly influences your decision-making. Extreme temperatures and the types of weather that come along with them, as well as their impact on your vehicle’s components, need to be understood in order to craft an effective fleet maintenance plan.
Historical performance and maintenance records should also be considered. This data can help identify which vehicles require more attention and which components are more likely to wear out. This can help you tailor your plan and optimize your time in the areas that need it the most.
3 Steps to Creating a Maintenance Schedule
Step 1: Inventory of Vehicles and Equipment
Document all vehicles in your fleet, noting their make, model, year, and any specific maintenance requirements. This is the foundation of your schedule, as it ensures that every vehicle's needs are accounted for and nothing is overlooked in the maintenance planning process.
Step 2: Vehicle Service Checklist
Develop a comprehensive list of maintenance tasks needed for each vehicle. This should include routine actions such as:
- Oil changes
- Tire rotations
- Brake inspections
- Filter replacements
Each task should be aligned with the manufacturer’s recommendations and maintenance frequency standards.
Step 3: Schedule and Tracking
Based on your prior assessment, assign a frequency to each maintenance task. You can define these by time intervals, distance driven, or engine hours. Using maintenance tracking software or even a simple spreadsheet keeps records up-to-date and ensures no vehicle goes unchecked.
The key to a good schedule is to integrate flexibility into your planning to accommodate emergency repairs and unexpected maintenance needs. This flexibility can help mitigate downtime by swiftly addressing any unforeseen issues that arise.
Training and Implementation
Proper training and explanation of the specifics of your preventive maintenance schedule are crucial for those managing a team. Each member needs to understand the schedule's importance and how to execute it. Implementation across the fleet should be systematic and carefully monitored to make sure the schedule is followed to a tee.
Effective training also involves regular refreshers and updates to maintenance procedures, including any new technologies you’re bringing into your operations. This ongoing education maintains high standards of service and ensures that your team is able to handle all types of heavy-duty vehicles and situations.
Monitoring and Adjusting
Continuous monitoring is essential to the effectiveness of your preventive maintenance schedule. This involves regular evaluations of maintenance logs, feedback from technicians, and analysis of performance data. This data can reveal patterns that require adjustments in the maintenance tasks or their frequency.
Changes in fleet size or vehicle usage, such as increased delivery routes or new operational terrains, also need to be accounted for and your schedule adjusted accordingly.
Implementing downtime reduction strategies and long-term maintenance strategies can further increase your operations' reliability and efficiency. Regularly revisiting and revising the maintenance schedule based on actual data and feedback allows you to alter and evolve it to fit your needs.
Final Thoughts
Creating and adhering to a comprehensive preventive maintenance schedule is essential for maximizing the uptime, safety, and cost-effectiveness of heavy-duty vehicles. By following the steps we’ve outlined above, you can ensure that your vehicles remain reliable and efficient. This guideline should only be the beginning; you should look to continuously improve your maintenance practices.
Remember, a well-maintained vehicle is the backbone of efficient fleet operations. With correct planning, you can build a maintenance schedule that lasts and evolves with your business needs.
Schedule Service at a location near you TODAY!
Contact the truck repair shop nearest you with any questions, quote requests, and to schedule service.